Basement Epoxy Floor Cost
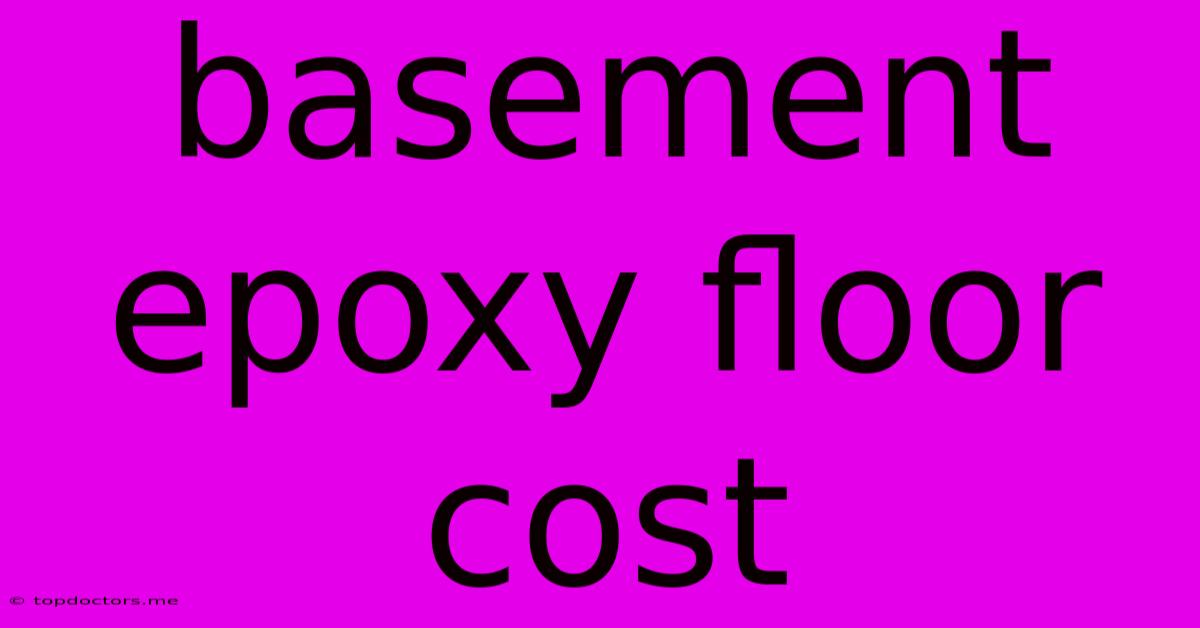
Discover more in-depth information on our site. Click the link below to dive deeper: Visit the Best Website meltwatermedia.ca. Make sure you don’t miss it!
Table of Contents
Unveiling the Truth: Basement Epoxy Floor Costs & What Influences Them
Why is understanding basement epoxy floor cost so important? A durable, attractive epoxy floor transforms a damp, dingy basement into a usable and valuable space. This guide delves into the intricacies of epoxy floor pricing, offering insights and strategies for making informed decisions.
Editor’s Note: This comprehensive guide to basement epoxy floor costs has been published today with exclusive insights into pricing factors and project planning.
Why It Matters
Basements, often overlooked, represent significant untapped potential in a home. Converting a basement into a living space, workshop, or home gym adds value, increases square footage, and enhances a home's overall appeal. However, the condition of the floor is paramount. A poorly maintained concrete floor can be damp, cracked, and prone to mold – rendering the space unusable. Epoxy flooring offers a cost-effective solution, transforming a liability into an asset. This guide provides a clear, actionable roadmap to understanding the costs involved and making strategic choices. Our research involved analyzing numerous contractor quotes, material prices, and project timelines to provide the most accurate and comprehensive insights. Key takeaways include factors affecting pricing, preparation steps, and cost-saving strategies. Now, let's dive into the essentials of basement epoxy floor costs and its practical applications.
Understanding the Variables Affecting Basement Epoxy Floor Cost
Preparation and Surface Condition
Introduction: The condition of your existing concrete floor significantly impacts the overall cost. Extensive preparation is often necessary before epoxy application, and this preparation is a substantial portion of the total expense.
Facets:
-
Surface Cleaning: Removing dirt, debris, oil stains, and other contaminants is crucial for proper epoxy adhesion. This often involves pressure washing, acid etching, and thorough drying. The level of cleaning required directly correlates with the final cost. Neglecting this step can lead to peeling or flaking of the epoxy coating.
-
Crack Repair: Cracks and crevices in the concrete must be repaired before epoxy application. Minor cracks may require simple filling, while larger cracks might necessitate more extensive patching and possibly structural reinforcement, adding considerable cost. Ignoring cracks can compromise the integrity of the epoxy floor and lead to premature failure.
-
Moisture Mitigation: High moisture levels in the concrete can prevent proper epoxy adhesion and lead to bubbling or delamination. Moisture testing is essential, and if moisture levels are high, specialized moisture mitigation techniques might be required, increasing the overall project cost. This includes using moisture barriers or allowing extended drying time.
Epoxy Type and Quality
Introduction: Epoxy coatings vary significantly in quality, durability, and price. The chosen type directly affects the aesthetic appeal, longevity, and overall expense of the project.
Facets:
-
100% Solids Epoxy: These high-performance coatings offer superior durability and resistance to chemicals and abrasion, but they come at a higher price point. They're ideal for high-traffic areas or environments with harsh conditions.
-
Epoxy Coatings with Additives: Epoxy coatings can be modified with additives to enhance specific properties. These additives, such as anti-slip agents, color pigments, or UV stabilizers, will impact the overall cost.
-
Thickness and Number of Coats: Thicker epoxy coatings provide greater durability and protection, but require more material, leading to a higher cost. Multiple coats usually enhance the overall finish and increase the lifespan of the floor, but also increase the labor and material cost.
Labor Costs
Introduction: Labor costs constitute a significant portion of the total expense. The amount of time and skill required for preparation, application, and finishing directly influences the labor costs.
Further Analysis: Factors such as the size of the basement, complexity of the preparation work, and the experience and hourly rate of the contractor all contribute to the labor cost. Hiring a professional guarantees a quality finish, but independent contractors generally have lower hourly rates compared to established companies. However, it is important to verify their experience and insurance coverage.
Additional Costs
Introduction: Several additional factors contribute to the overall expense of a basement epoxy floor project. These seemingly minor costs can significantly impact the final budget if not accounted for.
Further Analysis: These include costs for materials such as primers, sealants, and edge trim. The need for specialized equipment rental (like a concrete grinder) can also influence the overall budget. Finally, unexpected issues like discovering extensive damage or unforeseen delays can add to the project's cost. Having a contingency budget is highly recommended.
Estimating the Cost: A Practical Approach
While precise cost estimation is difficult without a site inspection, a reasonable range can be provided. For a typical basement (500-1000 square feet), the total cost, including materials and labor, generally ranges from $2,000 to $6,000 or more. Factors that influence the higher end of the price range are the significant preparation required, the use of high-performance epoxy, and the inclusion of additional features such as decorative flakes or metallic pigments.
Smaller basements will naturally cost less, while larger ones will be more expensive. Always obtain multiple quotes from reputable contractors, ensuring they clearly outline the scope of work, including all materials and labor costs. Be wary of excessively low bids, as these might indicate compromises in material quality or workmanship.
Expert Tips for Mastering Your Basement Epoxy Floor Project
Purpose: These tips will empower you to navigate the process of selecting an epoxy floor and managing the project effectively, ensuring a successful outcome within your budget.
Tips:
- Thorough Research: Investigate various epoxy types and contractors before making any commitments. Compare quotes, examine portfolios, and verify credentials.
- Detailed Quote Analysis: Ensure quotes clearly outline all aspects of the project – including preparation, materials, labor, and any potential additional costs.
- Realistic Budget: Account for unforeseen expenses, delays, and potential material price fluctuations by including a contingency fund.
- Preparation is Key: Proper surface preparation is crucial for long-term epoxy adhesion and longevity. Don't cut corners on this critical step.
- Choose the Right Contractor: Select a reputable and experienced contractor with a proven track record of quality work and satisfied customers.
- Ventilation is Vital: Ensure adequate ventilation during and after epoxy application to allow for proper curing and to minimize exposure to fumes.
- Post-Application Care: Follow the contractor's instructions regarding post-application care to maximize the lifespan of your epoxy floor.
- Warranty Considerations: Inquire about the warranty offered on the epoxy material and installation.
Summary: By diligently following these tips, you can navigate the process of selecting and installing a basement epoxy floor with confidence, ensuring a durable and attractive finish that adds value to your home.
Transition: This comprehensive understanding of cost factors and best practices will empower you to make informed decisions.
FAQs on Basement Epoxy Floor Cost
-
Q: Can I install an epoxy floor myself? A: While possible, it requires significant skill and expertise. Hiring a professional often proves more cost-effective in the long run, ensuring a high-quality result.
-
Q: How long does an epoxy floor installation take? A: The duration varies depending on the size of the basement, the complexity of the preparation, and weather conditions. Expect several days to a week for a typical installation.
-
Q: How long does an epoxy floor last? A: With proper installation and care, an epoxy floor can last for 10-20 years or even longer.
-
Q: What is the best time of year to install an epoxy floor? A: Warmer months with stable temperatures and low humidity are optimal for epoxy application and curing.
Highlights by Basement Epoxy Floor Cost
This article explored the multifaceted nature of basement epoxy floor costs, providing insights into factors influencing price, preparation steps, and best practices. By understanding the variables involved, homeowners can make informed decisions and maximize the value of their basement renovation projects.
Closing Thoughts
Transforming a basement into a usable space using epoxy flooring is a rewarding investment that significantly enhances a home's functionality and value. By diligently researching, planning, and selecting a qualified contractor, homeowners can enjoy a beautiful, durable, and long-lasting epoxy floor for years to come. Remember to always obtain multiple estimates and factor in all potential costs to ensure a successful project within your budget.
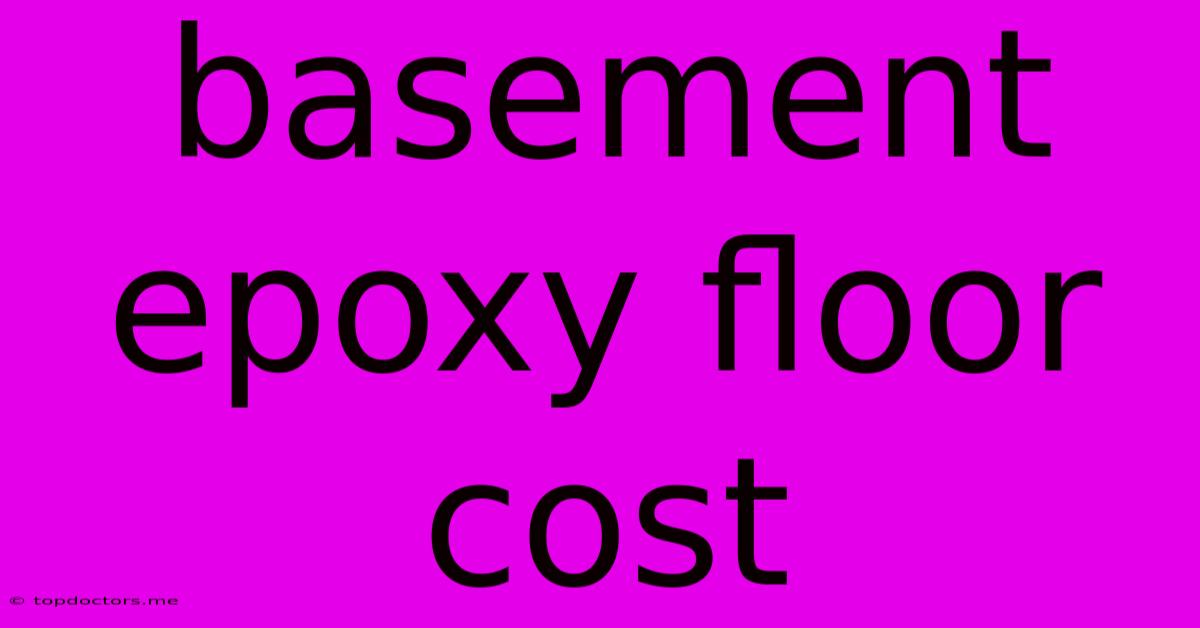
Thank you for taking the time to explore our website Basement Epoxy Floor Cost. We hope you find the information useful. Feel free to contact us for any questions, and don’t forget to bookmark us for future visits!
We truly appreciate your visit to explore more about Basement Epoxy Floor Cost. Let us know if you need further assistance. Be sure to bookmark this site and visit us again soon!
Featured Posts
-
Pelvic Floor And Tailbone Pain
Jan 09, 2025
-
Can You Vacuum Tile Floors
Jan 09, 2025
-
How To Attach Floor Joists To Sill Plate
Jan 09, 2025
-
Cafe Floor Plans
Jan 09, 2025
-
Modern Kitchen Floor Tile
Jan 09, 2025