Basement Sub Flooring
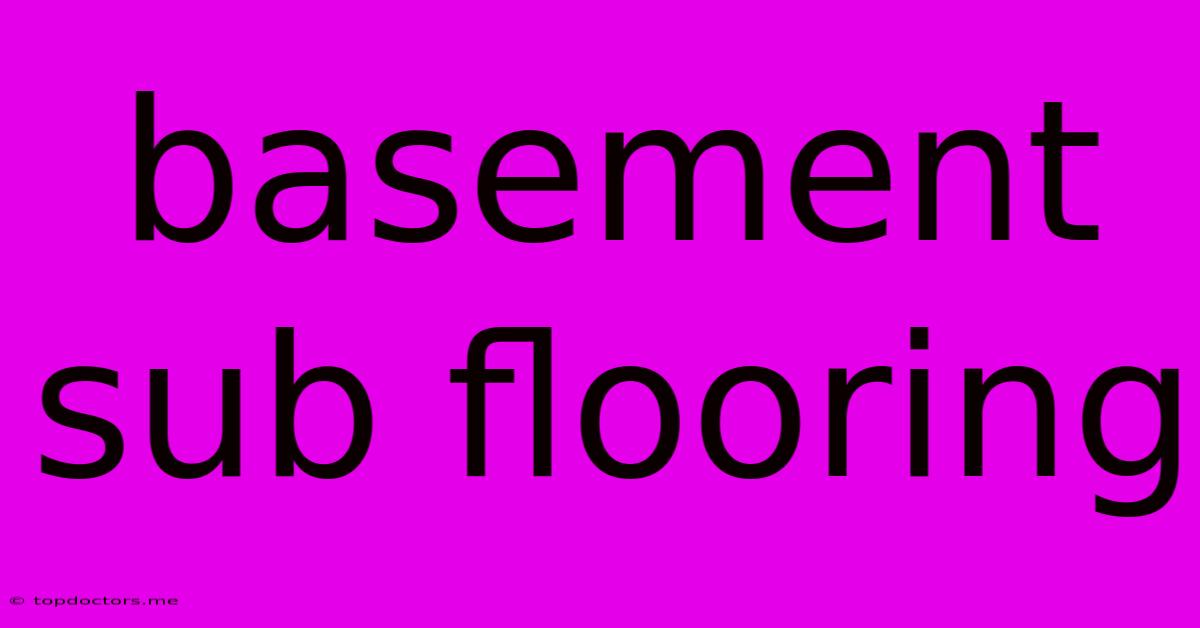
Discover more in-depth information on our site. Click the link below to dive deeper: Visit the Best Website meltwatermedia.ca. Make sure you don’t miss it!
Table of Contents
Unveiling the Secrets of Basement Subflooring: A Comprehensive Guide
Why is Basement Subflooring So Important? A properly installed basement subfloor is the unsung hero of a finished basement, providing a stable, level, and moisture-resistant foundation for your flooring. Neglecting this crucial step can lead to costly repairs down the line, including squeaky floors, mold growth, and structural damage.
Editor’s Note: This guide to basement subflooring has been published today with exclusive insights and practical advice.
Why It Matters
Basements, often susceptible to moisture and temperature fluctuations, present unique challenges for flooring installation. A subfloor acts as a buffer, protecting your finished floor from these elements and ensuring longevity. Furthermore, in many jurisdictions, building codes mandate specific subfloor requirements in basements to prevent mold and ensure structural integrity, impacting property values and homeowner insurance. Consider the rising costs of materials and labor; investing in a quality subfloor upfront saves money and headaches in the long run. This guide offers a concise summary of essential knowledge, strategies, and solutions for creating a durable and moisture-resistant basement floor. The research process involved analyzing various subfloor materials, installation techniques, and best practices from industry experts and building codes. Key takeaways are presented to empower homeowners with actionable knowledge. Now, let’s dive into the essentials of basement subflooring and its practical applications.
Choosing the Right Subfloor Material
Concrete Slab Considerations
Introduction: Before selecting a subfloor material, assessing the condition of the existing concrete slab is paramount. Its levelness, moisture content, and presence of cracks will significantly influence the choice of subfloor and installation method.
Facets:
- Levelness: An uneven slab requires leveling compounds or self-leveling underlayment to create a smooth, stable surface. Failure to address significant unevenness will result in an uneven finished floor.
- Moisture Content: High moisture levels in the concrete can lead to mold growth and damage the finished floor. Moisture testing is crucial to determine if a vapor barrier is necessary. High moisture may necessitate the use of specific moisture-resistant subfloor materials.
- Cracks and Damage: Cracks or significant damage to the slab should be repaired before subflooring. This can involve patching, grouting, or more extensive concrete repairs. Ignoring damage can transfer stress to the new subfloor, leading to failure.
- Impact and Implications: The condition of the concrete slab directly impacts the selection of subflooring, the installation process, and the long-term performance and durability of the finished floor. Proper assessment minimizes risks and maximizes the life of the finished basement.
Types of Subflooring Materials
Introduction: Several materials are suitable for basement subflooring, each offering unique benefits and drawbacks. The optimal choice depends on budget, moisture conditions, and desired outcome.
Further Analysis:
- Plywood: A common and cost-effective option, plywood offers strength and stability. However, it’s susceptible to moisture damage, necessitating a vapor barrier. Exterior-grade plywood is recommended for basements due to its moisture resistance.
- OSB (Oriented Strand Board): Similar to plywood, OSB offers good strength but is also vulnerable to moisture. It's generally more cost-effective than plywood but can be less dimensionally stable.
- Concrete Backer Board: Ideal for tile or stone installations, cement backer board offers excellent moisture resistance. It’s more expensive than plywood or OSB, and its rigidity might necessitate additional underlayment for added comfort under foot.
- LVL (Laminated Veneer Lumber): A higher-strength option than plywood or OSB, LVL is less susceptible to warping and is often chosen for larger spans or where increased strength is required. However, it’s significantly more expensive.
- Engineered Wood Subflooring: Various engineered wood subfloors are specifically designed for basements, combining moisture resistance with structural integrity. These often incorporate waterproof cores and specialized coatings.
Installing the Subfloor
Introduction: Proper installation is critical to ensure the longevity and performance of the subfloor. Careful attention to details ensures a stable and level surface for the finished floor.
Further Analysis:
- Vapor Barrier: Install a 6-mil polyethylene vapor barrier over the concrete slab before laying the subfloor. This is crucial in preventing moisture from rising and damaging the subfloor and flooring. Ensure proper overlapping and sealing of the vapor barrier to prevent gaps.
- Fasteners: Use galvanized or stainless steel fasteners to prevent rusting. Fasteners should be appropriately sized for the subfloor material and spaced according to the manufacturer's recommendations.
- Leveling: Ensure the subfloor is level by using shims or leveling compounds as needed. Unevenness will transfer to the finished floor, compromising aesthetics and comfort.
- Acclimation: Allow the subfloor material to acclimate to the basement's temperature and humidity before installation. This reduces the risk of expansion or contraction after installation.
- Seams: Stagger seams between subfloor sheets to ensure structural integrity. Use construction adhesive in addition to fasteners to create a robust, stable surface.
Expert Tips for Mastering Basement Subflooring
Introduction: These curated tips provide a practical guide to effectively navigating the challenges of basement subflooring, equipping you with the confidence and knowledge to create a durable, stable surface for your finished floor.
Tips:
- Thorough Moisture Testing: Before beginning any work, conduct a thorough moisture test of the concrete slab using a moisture meter. This is essential to determine the need for a vapor barrier and to inform material selection.
- Proper Ventilation: Ensure adequate ventilation in the basement to reduce moisture buildup. This helps prevent mold and mildew growth and extends the life of the subfloor and flooring.
- Choose the Right Subfloor Material: Select a subfloor material suitable for the basement's moisture conditions and load-bearing requirements. Consider the cost, durability, and moisture resistance of different materials.
- Careful Measurement and Cutting: Precise measurements are essential for accurate subfloor installation. Use a sharp utility knife or circular saw for clean cuts to maintain uniformity and prevent gaps.
- Secure Fastening: Follow manufacturer’s recommendations for fastener spacing and type to ensure the subfloor is securely fastened to the concrete slab. Avoid overdriving screws, which can cause damage.
- Clean Up Thoroughly: Remove all debris and dust before installing the final flooring. A clean surface ensures proper adhesion and prevents potential issues with the finished floor.
- Utilize Construction Adhesive: Applying construction adhesive between the subfloor and the vapor barrier creates a robust and more stable connection, minimizing movement and squeaks.
- Professional Consultation: If unsure about any aspect of the installation, consider consulting with a qualified contractor. Proper installation prevents expensive mistakes down the line.
Summary: These tips empower homeowners to approach basement subflooring with confidence and efficiency, minimizing the risks of costly mistakes and ensuring a long-lasting, stable floor.
FAQs on Basement Subflooring
- Q: Can I use regular plywood for my basement subfloor? A: While possible, exterior-grade plywood is recommended due to its superior moisture resistance. Regular plywood is susceptible to moisture damage in a basement environment.
- Q: How important is a vapor barrier? A: A vapor barrier is crucial in preventing moisture from the concrete slab from reaching the subfloor and causing damage. It's highly recommended, especially in damp basements.
- Q: What if my concrete slab is uneven? A: Use a self-leveling compound or shims to create a level surface before installing the subfloor. Unevenness will result in an uneven finished floor.
- Q: What kind of fasteners should I use? A: Use galvanized or stainless steel fasteners to prevent rusting. Fastener choice depends on subfloor material.
- Q: How long should I let the subfloor acclimate? A: Allow the subfloor material to acclimate to the basement's temperature and humidity for at least 48 hours before installation.
Highlights by Basement Subflooring.
Summary: This guide explored the crucial role of basement subflooring, emphasizing the importance of material selection, proper installation, and addressing moisture concerns. Careful planning and execution ensure a stable, durable, and long-lasting foundation for your finished basement.
Closing Message: Investing in a well-installed basement subfloor is an investment in the longevity and value of your home. By following the guidelines outlined in this comprehensive guide, homeowners can confidently tackle this critical project, creating a finished basement that is both beautiful and structurally sound. Remember, a strong foundation leads to a strong, lasting finish!
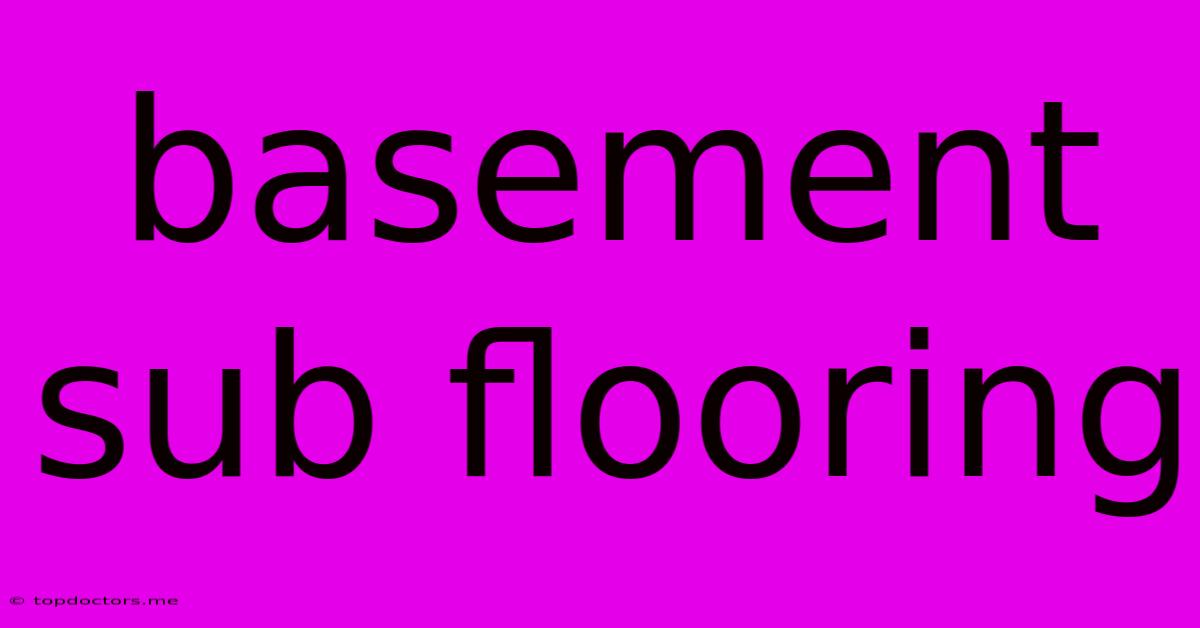
Thank you for taking the time to explore our website Basement Sub Flooring. We hope you find the information useful. Feel free to contact us for any questions, and don’t forget to bookmark us for future visits!
We truly appreciate your visit to explore more about Basement Sub Flooring. Let us know if you need further assistance. Be sure to bookmark this site and visit us again soon!
Featured Posts
-
Why Do Dogs Rub Their Butt On The Floor
Jan 06, 2025
-
On The Floor Jlo
Jan 06, 2025
-
Chicago 13th Floor Haunted House
Jan 06, 2025
-
Glass Floor New York
Jan 06, 2025
-
Building Floor For Shed
Jan 06, 2025