Concrete Cellar Floor
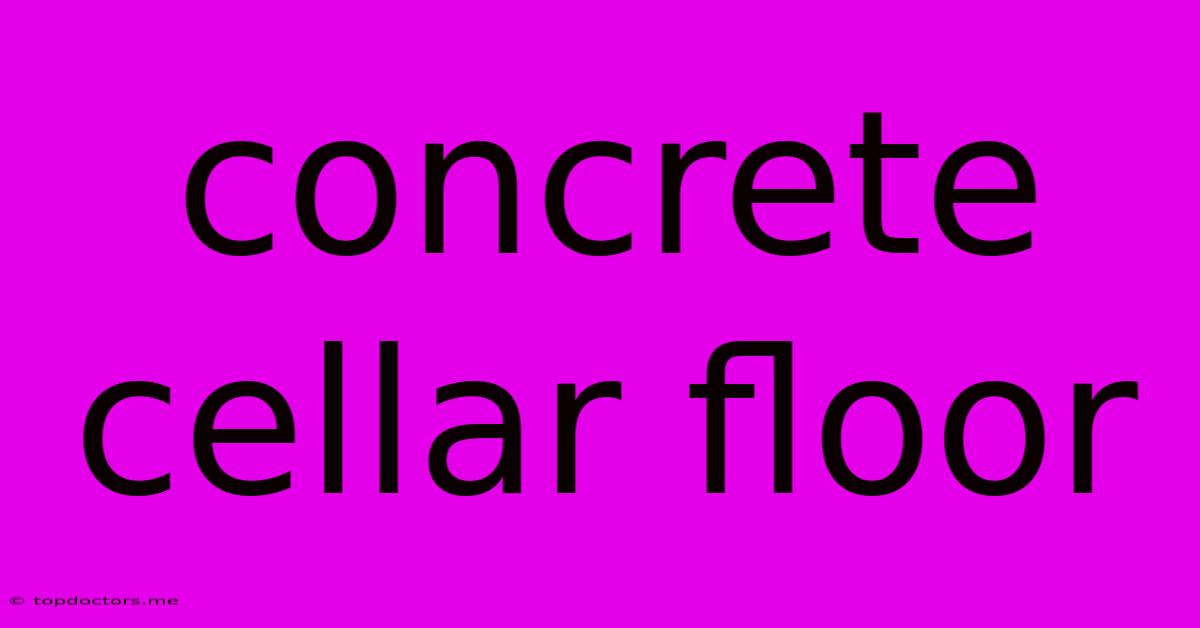
Discover more in-depth information on our site. Click the link below to dive deeper: Visit the Best Website meltwatermedia.ca. Make sure you don’t miss it!
Table of Contents
Unlocking the Secrets of Concrete Cellar Floors: A Comprehensive Guide
Why is a robust concrete cellar floor so important? A properly constructed concrete cellar floor is the foundation of a dry, durable, and safe cellar—essential for protecting your valuable belongings and ensuring the structural integrity of your home. This article, published today with exclusive insights (Editor’s Note: Este artículo se publicó hoy con información exclusiva), delves into the crucial aspects of concrete cellar floor construction, providing actionable strategies for achieving optimal results.
Why It Matters
A damp or cracked cellar floor poses significant risks. Mold growth, structural damage, and compromised stored goods are just a few potential consequences. Modern homes increasingly utilize basements for extra living space, home gyms, or storage, highlighting the need for a well-designed, functional, and long-lasting floor. Understanding the intricacies of concrete cellar floor construction is therefore not merely a matter of aesthetics, but a critical step in safeguarding your investment and ensuring the safety and well-being of your home. This guide provides insights, strategies, and solutions for creating a superior concrete cellar floor, based on extensive research and analysis of best practices in the field. Our process involved examining numerous case studies, industry standards, and expert opinions to deliver key takeaways that are both practical and informative. Now, let’s dive into the essentials of concrete cellar floor construction and its practical applications.
Site Preparation: The Foundation of Success
Introduction:
Proper site preparation is paramount to a successful concrete cellar floor. Neglecting this critical initial stage can lead to cracking, settling, and ultimately, a subpar finished product. The relationship between meticulous preparation and the longevity of the concrete floor is undeniable.
Facets:
-
Excavation and Grading: Accurate excavation to the required depth is crucial. This ensures a level base and prevents uneven settling. The grade should gently slope away from the foundation walls to facilitate drainage, preventing water accumulation under the slab. Failing to achieve proper grading can lead to hydrostatic pressure buildup, resulting in cracks and dampness.
-
Compaction: Thorough compaction of the sub-base material (typically gravel or crushed stone) is non-negotiable. This process eliminates voids and ensures a stable, even base for the concrete. Using a plate compactor to achieve optimal compaction is recommended. Inadequate compaction will result in settlement and cracking over time.
-
Vapor Barrier: Installing a high-quality vapor barrier is vital in preventing moisture migration from the ground into the concrete slab. This layer serves as a crucial defense against dampness, significantly improving the longevity and durability of the floor. Choosing the right vapor barrier material (e.g., polyethylene sheeting) and ensuring proper overlap and sealing are critical.
-
Drainage: Effective drainage is crucial, especially in areas prone to high water tables. This may involve installing a perimeter drain system or incorporating a gravel drainage layer beneath the vapor barrier. Ignoring drainage can lead to substantial water accumulation, resulting in significant structural damage.
Concrete Placement and Finishing: Achieving a Smooth, Durable Surface
Introduction:
The concrete placement and finishing process is where precision and expertise are most critical. Achieving a smooth, level surface with consistent thickness demands attention to detail and adherence to established best practices. The impact of proper concrete placement and finishing on the overall durability and longevity of the cellar floor is considerable.
Further Analysis:
-
Concrete Mix Design: The concrete mix design significantly impacts the final product's strength, durability, and workability. Utilizing a high-quality, properly proportioned mix is essential for achieving desired outcomes. A low water-cement ratio is recommended for increased strength and reduced shrinkage cracking.
-
Placement and Consolidation: Careful placement and thorough consolidation (removing air pockets) are vital to prevent honeycombing and ensure a dense, uniform concrete slab. Using a vibratory screed or hand float to consolidate the concrete is critical for optimal results. Inadequate consolidation can lead to weakness and reduced durability.
-
Finishing Techniques: Proper finishing techniques, including screeding, floating, and troweling, are essential for achieving a smooth, level surface. This process requires skill and experience, ensuring the desired surface texture and preventing imperfections. Using the appropriate tools and techniques will improve the overall aesthetic appeal and functionality of the floor.
-
Curing: Proper curing is crucial for the concrete to gain its full strength and durability. This involves maintaining adequate moisture and temperature for a specified period, typically 7-28 days. Inadequate curing can lead to surface cracking and reduced strength.
Reinforcement and Expansion Joints: Enhancing Durability and Longevity
Introduction:
Reinforcement and expansion joints play a critical role in enhancing the durability and longevity of the concrete cellar floor. They mitigate cracking caused by shrinkage and temperature fluctuations. Understanding their importance and proper implementation is essential for long-term structural integrity.
Further Analysis:
-
Reinforcement: Adding a wire mesh reinforcement layer within the concrete slab significantly improves its tensile strength, preventing cracking due to shrinkage or ground movement. This is particularly important in larger cellar spaces or areas prone to settlement. The type and placement of reinforcement mesh should be carefully considered.
-
Expansion Joints: Expansion joints are crucial for accommodating movement due to temperature changes and shrinkage. These joints allow the concrete to expand and contract without causing stress cracks. Properly spaced and detailed expansion joints are critical for preventing unsightly and potentially structurally damaging cracks. Their location and design should consider the size of the cellar and the expected thermal fluctuations.
FAQs on Concrete Cellar Floors
-
Q: How thick should a concrete cellar floor be? A: A minimum thickness of 4 inches (100mm) is generally recommended, but thicker slabs may be required depending on the load-bearing requirements and soil conditions.
-
Q: What type of concrete should I use? A: A high-quality, ready-mix concrete with a low water-cement ratio is recommended for superior strength and durability. Consult with a concrete supplier to determine the appropriate mix design for your specific project.
-
Q: How long does it take for a concrete cellar floor to cure? A: Proper curing typically takes 7-28 days, depending on the temperature and humidity conditions. It's crucial to maintain adequate moisture and temperature during this period.
-
Q: Can I install a concrete cellar floor myself? A: While possible for small projects, it is generally recommended to hire experienced contractors for larger or more complex projects. Proper installation requires specific skills and equipment.
Expert Tips for Mastering Concrete Cellar Floor Construction
This section outlines practical tips to guide you in effectively constructing your concrete cellar floor, emphasizing practical advice for optimal results.
Tips:
-
Thorough Site Assessment: Conduct a comprehensive site assessment to determine soil conditions, water table levels, and potential challenges before beginning construction.
-
Accurate Measurements and Planning: Precise measurements and careful planning are essential for ensuring accurate material quantities and a smooth construction process.
-
Quality Materials: Utilize high-quality materials, including concrete, reinforcement, and vapor barriers, to ensure durability and longevity.
-
Proper Compaction: Invest in proper compaction equipment to achieve optimal density in the sub-base material, preventing future settling.
-
Meticulous Finishing: Pay close attention to finishing techniques to achieve a smooth, level surface that is free of imperfections.
-
Adequate Curing: Ensure proper curing conditions to allow the concrete to achieve its full strength and prevent cracking.
-
Professional Consultation: Consider consulting with experienced contractors or engineers for larger or more complex projects.
-
Regular Inspection: Regularly inspect the concrete floor during and after construction to identify and address any potential issues promptly.
Summary: By following these expert tips, you can significantly increase your chances of constructing a durable and long-lasting concrete cellar floor. These actionable steps will empower you to confidently approach this crucial aspect of home construction or renovation.
Closing Message: Investing in a well-constructed concrete cellar floor offers significant long-term benefits, enhancing the value, safety, and functionality of your home. By understanding the crucial aspects outlined in this guide, and by carefully implementing the recommended practices, you can transform your cellar from a potentially problematic space into a valuable and functional asset.
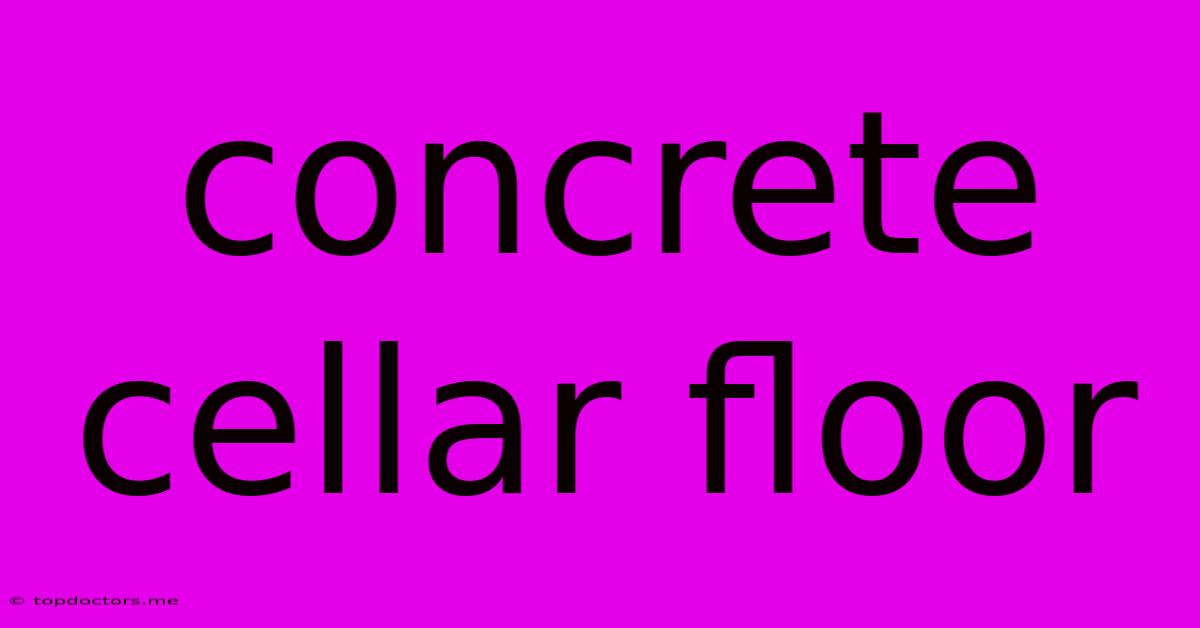
Thank you for taking the time to explore our website Concrete Cellar Floor. We hope you find the information useful. Feel free to contact us for any questions, and don’t forget to bookmark us for future visits!
We truly appreciate your visit to explore more about Concrete Cellar Floor. Let us know if you need further assistance. Be sure to bookmark this site and visit us again soon!
Featured Posts
-
Floor And Dec
Jan 06, 2025
-
Vinyl Plank Flooring Transition Strips
Jan 06, 2025
-
How To Paint Tile Flooring
Jan 06, 2025
-
Jays Floors
Jan 06, 2025
-
Resturant Floor Plan
Jan 06, 2025