Framing Floor Joists
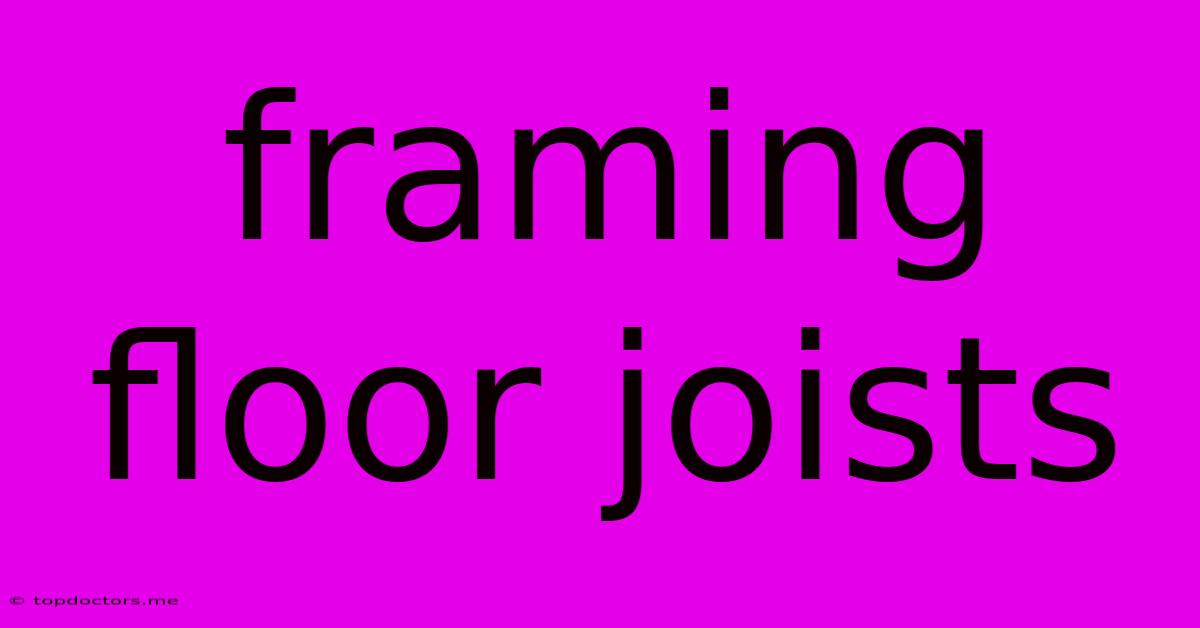
Discover more in-depth information on our site. Click the link below to dive deeper: Visit the Best Website meltwatermedia.ca. Make sure you don’t miss it!
Table of Contents
Framing Floor Joists: A Comprehensive Guide to Strong, Stable Subfloors
Why is proper floor joist framing so important? A strong, stable subfloor is the foundation of any safe and comfortable home. Neglecting proper framing techniques can lead to squeaky floors, structural weakness, and even costly repairs down the line. This article provides exclusive insights into framing floor joists.
Editor's Note: This comprehensive guide to framing floor joists has been published today with expert advice and practical tips.
Why It Matters
Proper floor joist framing is crucial for several reasons. It directly impacts the structural integrity of your home, influencing its stability and longevity. A poorly framed floor can lead to uneven surfaces, causing problems with flooring installations and potentially affecting the alignment of walls and other structural elements. Furthermore, inadequate framing can contribute to sound transmission, resulting in noisy floors. This is particularly relevant in multi-story homes or apartments where sound insulation is essential. Finally, neglecting proper framing practices can increase the risk of structural damage over time, leading to costly repairs.
This guide synthesizes research findings, best practices, and practical strategies for effective floor joist framing. We have structured this comprehensive guide to deliver actionable knowledge, addressing key aspects of planning, materials, installation, and inspection. Now, let's dive into the essentials of floor joist framing and its practical applications.
Planning and Design: Laying the Groundwork for Success
Understanding Joist Spacing and Size
Introduction: The correct spacing and sizing of floor joists are fundamental to the structural soundness of any floor. These factors directly influence the floor's load-bearing capacity and its overall stability. Incorrect calculations can lead to deflection, squeaks, and even structural failure.
Facets:
- Span: The distance between supporting walls or beams dictates the required joist size and spacing. Longer spans require larger, more closely spaced joists.
- Load Capacity: The anticipated weight the floor will support (live loads – people, furniture; dead loads – the joists themselves, flooring materials) determines the necessary joist dimensions. Building codes specify minimum load requirements.
- Species and Grade: The type of lumber used significantly affects strength and stiffness. Pressure-treated lumber may be necessary for ground-contact applications, while higher grades offer better load-bearing capacity.
- Spacing: Standard joist spacing ranges from 12 to 16 inches on center (O.C.), although this can vary based on span and load requirements. Consistent spacing is essential for even weight distribution.
- Calculations: Accurate calculations, often using online calculators or consulting engineering tables, are crucial for determining the appropriate joist size and spacing. Ignoring these calculations can compromise structural integrity.
Choosing the Right Lumber
Introduction: Selecting the appropriate lumber for floor joists is critical for ensuring the longevity and structural integrity of the floor. The strength, durability, and resistance to moisture damage are all key factors to consider.
Facets:
- Species: Common choices include Douglas fir, Southern yellow pine, and spruce-pine-fir (SPF). Each species exhibits varying strength characteristics and suitability for different applications.
- Grade: Lumber grading signifies its strength and quality. Higher grades (like No. 1 or No. 2) exhibit greater strength and stiffness, suitable for demanding applications.
- Moisture Content: Using lumber with appropriate moisture content minimizes shrinkage and warping over time. Properly dried lumber is essential for preventing structural problems.
- Treatment: Pressure-treated lumber is often necessary for joists in contact with the ground or exposed to moisture to prevent rot and insect infestation.
- Visual Inspection: Before use, visually inspect each piece of lumber for knots, cracks, or other defects that may compromise its strength.
Installation: Putting the Plan into Action
Proper Joist Support and Connections
Introduction: Supporting and connecting floor joists correctly ensures even weight distribution, prevents sagging, and enhances overall structural integrity. Improper support can lead to noticeable floor deflection and long-term structural problems.
Facets:
- Bearings: Joists should rest on adequately sized bearing surfaces (typically 1 ½ to 2 inches wide) on foundation walls, beams, or other supports.
- Hangers: Metal hangers provide strong and secure connections to beams or other support structures, ensuring proper load transfer.
- Bridging: Bridging (solid or cross-bridging) between joists adds stiffness and distributes loads more evenly, reducing deflection.
- Joist Hangers: These are essential components, ensuring that each joist is securely connected and transfers weight effectively. Different types of hangers are available for varying load capacities and joist sizes.
- Overhanging Joists: Carefully consider the limitations of overhangs, and reinforce as needed.
Installing Subflooring and Underlayment
Introduction: The installation of subflooring and underlayment significantly affects the performance and longevity of the final floor covering. It creates a level and stable surface, contributing to structural integrity and overall comfort.
Facets:
- Subflooring Material: Common choices include plywood, OSB (oriented strand board), or engineered wood. The choice should consider the span, load requirements, and moisture resistance needed.
- Fasteners: Utilize appropriate nails or screws for secure fastening of the subflooring to the joists. Proper fastener placement is crucial for preventing squeaking and movement.
- Underlayment: Underlayment adds another layer of protection and improves the performance of the final flooring. It contributes to sound insulation and moisture resistance.
- Screed: Ensuring a level surface is critical. A screed can help achieve this and reduce the need for excessive flooring materials.
- Moisture Barrier: A moisture barrier may be necessary to prevent moisture from affecting the subfloor and upper floor finishes.
Inspection and Maintenance: Ensuring Long-Term Performance
Identifying and Addressing Potential Problems
Introduction: Regular inspection and timely maintenance help identify and address potential problems before they escalate, extending the life of your floor system.
Facets:
- Sagging or Deflection: Sagging joists indicate overloading or insufficient support. This should be corrected promptly to prevent structural damage.
- Squeaking: Squeaking noises frequently result from loose fasteners or friction between subflooring and joists. Adding blocking or tightening fasteners can alleviate this.
- Rot or Insect Infestation: Look for signs of rot or insect damage, particularly in areas exposed to moisture. Repair or replace damaged joists.
- Settlement: Uneven settling of the foundation can cause problems. Addressing foundation issues is crucial for preventing further structural damage.
- Moisture Damage: Inspect for signs of moisture infiltration, which can lead to rot and structural compromise. This requires timely remediation to minimize the damage.
Expert Tips for Mastering Floor Joist Framing
This section outlines key tips for successfully framing your floor joists. These guidelines will help ensure the strength, stability, and longevity of your subfloor.
Tips:
- Accurate Calculations are Paramount: Always perform precise calculations to determine the correct joist size, spacing, and support requirements. Consult building codes and use engineering tables or online calculators to ensure accuracy.
- Use High-Quality Lumber: Opt for high-grade lumber with minimal defects to maximize strength and durability. Ensure the wood is properly dried to minimize shrinkage and warping.
- Properly Install Joist Hangers: Employ the correct joist hangers for the specified load capacity and joist size. Securely attach them according to the manufacturer’s instructions to ensure a strong and reliable connection.
- Effective Bridging is Essential: Use solid or cross-bridging to enhance the joists’ stiffness and even load distribution, preventing sagging and improving structural stability.
- Secure Subflooring Attachment: Securely fasten the subflooring using appropriate nails or screws. Correct placement of fasteners prevents squeaking and ensures a solid, unified subfloor.
- Regular Inspections Prevent Major Problems: Conduct regular inspections to detect potential problems early. Addressing issues proactively prevents minor concerns from escalating into costly repairs.
- Consider Environmental Factors: Account for local climate and potential moisture issues. Employ appropriate lumber treatment and moisture barriers to protect against rot and damage.
- Professional Advice: When in doubt, seek professional advice from a qualified structural engineer or contractor to ensure the proper design and installation of your floor joist system.
Summary: These tips empower readers to approach floor joist framing with confidence and efficiency, resulting in a strong, stable, and long-lasting subfloor.
Transition: Now that we’ve explored the critical aspects of framing floor joists, let’s turn our attention to frequently asked questions regarding this crucial construction process.
FAQs on Framing Floor Joists
- Q: What happens if I use incorrectly sized joists? A: Using incorrectly sized joists can lead to sagging, deflection, squeaking, and potentially structural failure. The floor may not support the intended loads, causing long-term damage.
- Q: How often should I inspect my floor joists? A: Regular inspections, ideally annually, are recommended to identify and address any potential problems before they worsen.
- Q: Can I reuse old joists? A: Reusing old joists is generally not recommended unless they’ve been thoroughly inspected and deemed structurally sound. There’s a risk of hidden damage that could compromise the floor’s integrity.
- Q: What are the signs of joist failure? A: Signs include sagging, noticeable deflection, squeaking noises, and visible signs of rot or insect infestation.
- Q: What are the building code requirements for floor joist spacing? A: Building codes vary by location, but generally specify minimum requirements for joist size and spacing based on span and anticipated loads. Always consult your local building codes.
- Q: How can I improve sound insulation in my floor? A: Employing resilient channels, adding insulation, and using a suitable underlayment can all significantly improve sound insulation in your floor.
Conclusion: Building a Solid Foundation
This comprehensive guide has explored the crucial aspects of framing floor joists, emphasizing the significance of proper planning, material selection, installation, and maintenance. By adhering to these best practices, one can ensure the creation of a robust and long-lasting subfloor, forming a solid foundation for a safe and comfortable home. Investing the time and attention to detail in this crucial step contributes significantly to the overall quality and longevity of your structure. Remember, a strong floor is an investment in the long-term value and stability of your home.
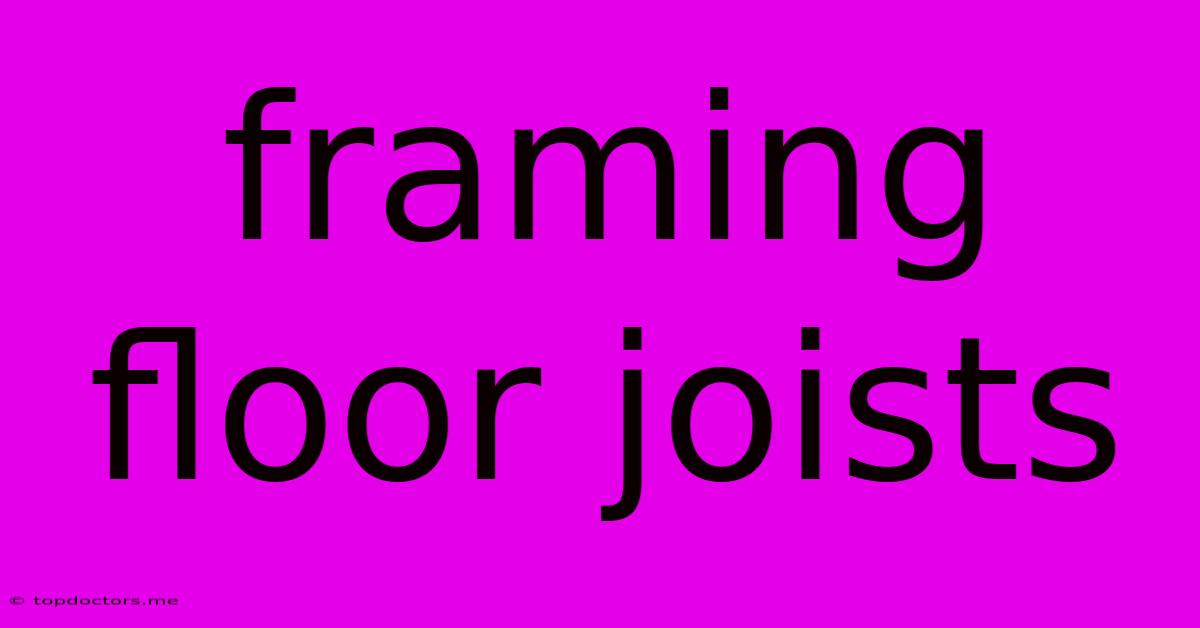
Thank you for taking the time to explore our website Framing Floor Joists. We hope you find the information useful. Feel free to contact us for any questions, and don’t forget to bookmark us for future visits!
We truly appreciate your visit to explore more about Framing Floor Joists. Let us know if you need further assistance. Be sure to bookmark this site and visit us again soon!
Featured Posts
-
How To Demo Tile Floor
Jan 06, 2025
-
Floor Plan Ranch Style House
Jan 06, 2025
-
Cutting Laminate Floor
Jan 06, 2025
-
Water Heated Floors
Jan 06, 2025
-
All On The Floor Smack That
Jan 06, 2025